Ring Main Unit (RMU): Working, Construction Detail & precommissiong & commissioning Test & Results
- Shadab Waseem
- Jun 28, 2023
- 8 min read
Updated: Oct 25, 2023
Introduction
Ring Main Unit (RMU) is a compact, self-contained, metal-enclosed switchgear unit that is commonly used in medium voltage distribution networks. It provides a reliable and flexible means of controlling and protecting electrical power distribution systems. The RMU consists of several components, including circuit breakers, disconnect switches, earthing switches, current transformers (CTs), voltage transformers (VTs), and protection relays.
Working Principle:
The working principle of an RMU involves the formation of a ring or loop network for power distribution. The incoming power supply is connected to the RMU, and from there, the power is distributed to various feeders or loads. The RMU allows for selective switching and protection of individual feeders. In normal operating conditions, the RMU routes power through the ring, while during faults or maintenance, the faulty section can be isolated by opening the associated circuit breakers.
Technical parameters of a Ring Main Unit (RMU)
The technical parameters of a Ring Main Unit (RMU) may vary depending on the specific manufacturer, model, and configuration. However, here are some common technical parameters associated with RMUs:
1. Rated Voltage: The rated voltage indicates the maximum voltage level that the RMU is designed to handle. Common voltage ratings for RMUs include 11 kV, 22 kV, and 33 kV.
2. Rated Current: The rated current specifies the maximum current that the RMU can safely carry. It is typically measured in amperes (A) and may vary based on the specific configuration and application.
3. Short-Circuit Current Rating: This parameter indicates the maximum level of short-circuit current that the RMU can safely interrupt without sustaining damage. It is essential for ensuring the proper coordination and protection of the electrical system.
4. Rated Frequency: The rated frequency refers to the frequency of the electrical power system to which the RMU is designed to be connected. It is commonly 50 Hz or 60 Hz, depending on the region.
5. Insulation Level: The insulation level specifies the dielectric strength of the RMU and its ability to withstand high voltage stresses. It is typically defined by parameters such as the power frequency withstand voltage and impulse voltage withstand level.
6. Number of Feeders: The RMU can accommodate a specific number of feeders or circuits. The number of feeders may vary, typically ranging from a few to several dozen, depending on the size and capacity of the RMU.
7. Type of Switchgear: RMUs may incorporate different types of switchgear, such as vacuum circuit breakers (VCBs), gas-insulated switchgear (GIS), or air-insulated switchgear (AIS). The type of switchgear impacts the performance, reliability, and maintenance requirements of the RMU.
8. Control and Protection Features: RMUs often include various control and protection features to ensure safe and reliable operation. These may include overcurrent protection, earth fault protection, fault detection systems, remote monitoring capabilities, and communication interfaces.
9. Enclosure Type: The RMU is typically housed in an enclosure to provide protection against environmental factors and unauthorized access. Enclosure types may include indoor or outdoor enclosures, metal-clad enclosures, or compact modular designs.
It's important to note that these technical parameters are general in nature, and actual specifications may vary significantly based on the specific RMU model and manufacturer. It is always recommended to refer to the manufacturer's documentation or contact the manufacturer directly for detailed technical specifications of a particular RMU.
Construction Part Details
Here are the key construction parts and their details:
1. Metal-Enclosed Housing: The RMU is housed within a robust metal enclosure, usually made of galvanized steel or stainless steel. This enclosure provides mechanical protection, electrical insulation, and safety for the internal components.
2. Circuit Breakers: RMUs incorporate circuit breakers to control and isolate electrical circuits. These circuit breakers can be of different types, such as vacuum, SF6, or air circuit breakers, depending on the specific design. They are responsible for interrupting the flow of current in case of faults or abnormal conditions.
3. Disconnect Switches: RMUs feature disconnect switches that provide a visible isolation point and allow safe maintenance and repairs. These switches are typically manually operated and are used to isolate specific feeders or sections of the distribution network.
4. Earthing Switches: Earthing switches are included in RMUs to provide a safe and reliable method for earthing or grounding the system. They ensure that the electrical equipment is effectively grounded for maintenance purposes or during fault conditions.
5. Current Transformers (CTs): CTs are used to measure the current flowing through the RMU. They convert high currents into proportional low currents, which are then used for metering, protection, and control purposes.
6. Voltage Transformers (VTs): VTs, also known as potential transformers, are employed to measure the voltage levels within the RMU. They step down the high voltage to a safe and measurable level, enabling accurate voltage measurements for monitoring and protection.
7. Protection Relays: RMUs are equipped with protection relays that monitor various parameters such as current, voltage, and frequency. These relays detect abnormal conditions, such as overcurrent, short circuits, or earth faults, and initiate appropriate actions, such as tripping the circuit breakers.
8. Busbars: Busbars are used to connect the various components within the RMU, allowing the flow of electrical current between them. They provide a reliable and low-resistance path for current transfer and distribution.
9. Insulation Materials: The internal components of the RMU, such as circuit breakers and busbars, are insulated using suitable materials to prevent electrical leakage and ensure safe operation. Common insulation materials include epoxy resins, SF6 gas, or vacuum.
10. Control and Monitoring Devices: RMUs may also incorporate control panels and monitoring devices for operators to control and monitor the system. These devices can include control switches, indicators, meters, and communication interfaces for remote monitoring and control.
Difference between Indoor & Outdoor RMU
Here's a comparative table showcasing different types of Ring Main Units (RMUs) based on the power distribution sector:
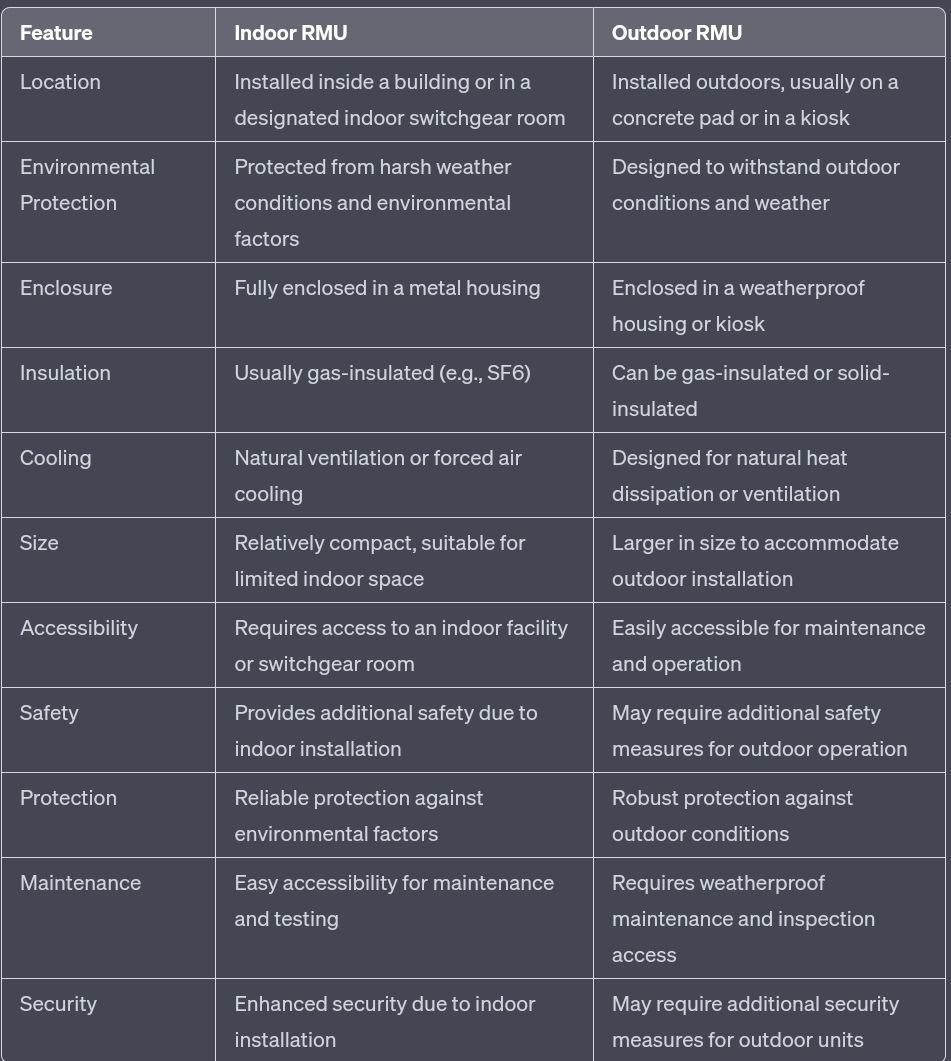
Differences and usage of 1W, 2W, 3W, and 4W RMU indoor breakers used in 11 kV power distribution sector
A) 1W RMU (Single-Way RMU):
- Description: A 1W RMU consists of a single breaker for controlling and protecting the power distribution network.
- Usage: 1W RMUs are commonly used in radial distribution networks where power flows in only one direction. They are suitable for applications where a single feeder or circuit needs to be controlled and protected.
B) 2W RMU (Two-Way RMU):
- Description: A 2W RMU comprises two breakers, allowing power to flow in two directions.
- Usage: 2W RMUs are used in ring-type or loop distribution networks where power can flow in both directions. They provide sectionalizing capability, allowing isolation and restoration of faulty sections without affecting the entire distribution network.
C) 3W RMU (Three-Way RMU):
- Description: A 3W RMU incorporates three breakers, enabling power flow in three directions.
- Usage: 3W RMUs are employed in networks where power can flow in multiple directions, such as multiple feeders or interconnected substations. They offer enhanced flexibility and sectionalizing capability, allowing isolation and restoration of faulty sections without disrupting the entire network.
D) 4W RMU (Four-Way RMU):
- Description: A 4W RMU consists of four breakers, facilitating power flow in four directions.
- Usage: 4W RMUs are used in complex distribution networks where power needs to be distributed to multiple feeders, substations, or interconnected grids. They provide extensive sectionalizing and interconnecting capabilities, allowing efficient network management and fault isolation.
The selection of the appropriate RMU type (1W, 2W, 3W, or 4W) depends on the specific network topology, power flow requirements, and the need for sectionalizing and isolation capabilities. It's crucial to conduct a thorough analysis of the distribution system to determine the suitable RMU configuration for efficient and reliable power distribution.
Interlocking systems:
An interlocking system in a Ring Main Unit (RMU) is a crucial safety feature designed to prevent unsafe operating conditions and ensure the correct sequence of operations. It involves a set of logical interlocks that control the switching operations within the RMU and maintain proper coordination between different components.
The primary purpose of an interlocking system is to prevent incorrect or unsafe operation of the RMU, which could lead to equipment damage, electrical faults, or harm to personnel. The interlocks are typically implemented through mechanical, electrical, or electronic means and are designed to enforce specific rules or conditions for the operation of the RMU.
Here are some common interlocking mechanisms found in RMUs:
1. Mechanical Interlocks: Mechanical interlocks use physical mechanisms, such as levers, rods, or interlocking keys, to prevent simultaneous or conflicting operations. For example, they can prevent the closing of a circuit breaker when the corresponding earthing switch is still in the closed position or the opening of a switch when there is voltage present.
2. Electrical Interlocks: Electrical interlocks employ electrical signals or contacts to enforce specific operating sequences. For instance, a circuit breaker may have electrical contacts that prevent it from closing if the associated isolator switch is not in the open position. Similarly, an interlock may be in place to prevent the closing of a switch if the earthing switch is not opened.
3. Logic-Based Interlocks: Logic-based interlocks utilize programmable logic controllers (PLCs) or microprocessor-based systems to implement complex interlocking logic. These systems can monitor various parameters, inputs, and conditions to determine the permissible sequence of operations. For example, a logic-based interlock can prevent the closing of a circuit breaker if there is an ongoing fault or if the voltage levels are outside the acceptable range.
The specific interlocking system in an RMU may vary depending on the manufacturer and model, as well as the intended application. The interlocking logic is typically designed in accordance with industry standards, safety regulations, and the specific requirements of the electrical network.
Interlocking systems are essential for maintaining the integrity and safety of the electrical system. They help prevent hazardous situations, such as inadvertently energizing or de-energizing a circuit, and ensure that operations are carried out in the correct sequence to minimize the risk of equipment damage or electrical faults.
Precommissioning and Electrical Commissioning Test Procedure :
1. Precommissioning Tests:
a. Visual Inspection: Verify that the RMU is installed correctly and all connections are properly made. Check for any physical damages or loose connections.
b. Mechanical Operation: Test the mechanical operation of the RMU, including the operation of circuit breakers, disconnect switches, and earthing switches.
c. Insulation Resistance Test: Measure the insulation resistance between phases and between each phase and earth using a megohmmeter. The typical acceptable value is above 1 Megaohm.
d. Continuity Test: Check the continuity of control and power circuits using a continuity tester or a multimeter. Ensure all connections are intact and have low resistance.
e. Secondary Injection Test: Perform secondary injection tests on protection relays to verify their correct operation. This includes testing overcurrent, earth fault, and differential relays.
2. Electrical Commissioning Tests:
a. Primary Injection Test: Conduct primary injection tests on circuit breakers to verify their tripping and closing characteristics. Measure the current and time taken for the circuit breaker to trip.
b. Timing Test: Perform timing tests on all the relays in the RMU. Measure the time taken for the relays to operate under different fault conditions and ensure they meet the specified time limits.
c. Dielectric Voltage Withstand Test: Apply a high voltage (typically 1.2 times the rated voltage) to the RMU for a specified duration to ensure its insulation can withstand the voltage without breakdown.
d. Partial Discharge Test: Carry out a partial discharge test to evaluate the insulation quality of the RMU. Measure the magnitude of partial discharges using suitable equipment.
e. Voltage Drop Test: Measure the voltage drop across the RMU under normal operating conditions to ensure it is within acceptable limits.
f. Current Transformer (CT) Ratio Test: Verify the accuracy of the CTs by injecting a known current and measuring the output. Compare the measured ratio with the rated ratio.
g. Voltage Transformer (VT) Ratio Test: Similar to the CT ratio test, inject a known voltage and measure the output to verify the accuracy of the VTs.
Reference Test Result Values:
The test result values for the RMU may vary depending on the specific manufacturer and model. It is crucial to refer to the manufacturer's documentation and specifications for the exact values. However, here are some general reference values that can be considered:
- Insulation Resistance: >1 Megaohm
- Timing Test: Relays should operate within specified time limits (e.g., <100 ms for certain relays)
- Dielectric Voltage Withstand Test: No breakdown or insulation failure at the specified test voltage
- Partial Discharge Test: Magnitude of partial discharges should be minimal (e.g., below a specified threshold)
- Voltage Drop Test: Voltage drop across the RMU should be within acceptable limits (e.g., <5% of the rated voltage)
- CT Ratio Test: Measured ratio should closely match the rated ratio with minimal error (e.g., within ±1%)
- VT Ratio Test: Measured ratio should closely match the rated ratio with minimal error (e.g., within ±1%)
Note: These reference values are provided as general guidelines. Always refer to the specific manufacturer's documentation for accurate reference values for the RMU being tested.
Very good